1.7: Cost Terminology
- Page ID
- 829
\( \newcommand{\vecs}[1]{\overset { \scriptstyle \rightharpoonup} {\mathbf{#1}} } \)
\( \newcommand{\vecd}[1]{\overset{-\!-\!\rightharpoonup}{\vphantom{a}\smash {#1}}} \)
\( \newcommand{\id}{\mathrm{id}}\) \( \newcommand{\Span}{\mathrm{span}}\)
( \newcommand{\kernel}{\mathrm{null}\,}\) \( \newcommand{\range}{\mathrm{range}\,}\)
\( \newcommand{\RealPart}{\mathrm{Re}}\) \( \newcommand{\ImaginaryPart}{\mathrm{Im}}\)
\( \newcommand{\Argument}{\mathrm{Arg}}\) \( \newcommand{\norm}[1]{\| #1 \|}\)
\( \newcommand{\inner}[2]{\langle #1, #2 \rangle}\)
\( \newcommand{\Span}{\mathrm{span}}\)
\( \newcommand{\id}{\mathrm{id}}\)
\( \newcommand{\Span}{\mathrm{span}}\)
\( \newcommand{\kernel}{\mathrm{null}\,}\)
\( \newcommand{\range}{\mathrm{range}\,}\)
\( \newcommand{\RealPart}{\mathrm{Re}}\)
\( \newcommand{\ImaginaryPart}{\mathrm{Im}}\)
\( \newcommand{\Argument}{\mathrm{Arg}}\)
\( \newcommand{\norm}[1]{\| #1 \|}\)
\( \newcommand{\inner}[2]{\langle #1, #2 \rangle}\)
\( \newcommand{\Span}{\mathrm{span}}\) \( \newcommand{\AA}{\unicode[.8,0]{x212B}}\)
\( \newcommand{\vectorA}[1]{\vec{#1}} % arrow\)
\( \newcommand{\vectorAt}[1]{\vec{\text{#1}}} % arrow\)
\( \newcommand{\vectorB}[1]{\overset { \scriptstyle \rightharpoonup} {\mathbf{#1}} } \)
\( \newcommand{\vectorC}[1]{\textbf{#1}} \)
\( \newcommand{\vectorD}[1]{\overrightarrow{#1}} \)
\( \newcommand{\vectorDt}[1]{\overrightarrow{\text{#1}}} \)
\( \newcommand{\vectE}[1]{\overset{-\!-\!\rightharpoonup}{\vphantom{a}\smash{\mathbf {#1}}}} \)
\( \newcommand{\vecs}[1]{\overset { \scriptstyle \rightharpoonup} {\mathbf{#1}} } \)
\( \newcommand{\vecd}[1]{\overset{-\!-\!\rightharpoonup}{\vphantom{a}\smash {#1}}} \)
\(\newcommand{\avec}{\mathbf a}\) \(\newcommand{\bvec}{\mathbf b}\) \(\newcommand{\cvec}{\mathbf c}\) \(\newcommand{\dvec}{\mathbf d}\) \(\newcommand{\dtil}{\widetilde{\mathbf d}}\) \(\newcommand{\evec}{\mathbf e}\) \(\newcommand{\fvec}{\mathbf f}\) \(\newcommand{\nvec}{\mathbf n}\) \(\newcommand{\pvec}{\mathbf p}\) \(\newcommand{\qvec}{\mathbf q}\) \(\newcommand{\svec}{\mathbf s}\) \(\newcommand{\tvec}{\mathbf t}\) \(\newcommand{\uvec}{\mathbf u}\) \(\newcommand{\vvec}{\mathbf v}\) \(\newcommand{\wvec}{\mathbf w}\) \(\newcommand{\xvec}{\mathbf x}\) \(\newcommand{\yvec}{\mathbf y}\) \(\newcommand{\zvec}{\mathbf z}\) \(\newcommand{\rvec}{\mathbf r}\) \(\newcommand{\mvec}{\mathbf m}\) \(\newcommand{\zerovec}{\mathbf 0}\) \(\newcommand{\onevec}{\mathbf 1}\) \(\newcommand{\real}{\mathbb R}\) \(\newcommand{\twovec}[2]{\left[\begin{array}{r}#1 \\ #2 \end{array}\right]}\) \(\newcommand{\ctwovec}[2]{\left[\begin{array}{c}#1 \\ #2 \end{array}\right]}\) \(\newcommand{\threevec}[3]{\left[\begin{array}{r}#1 \\ #2 \\ #3 \end{array}\right]}\) \(\newcommand{\cthreevec}[3]{\left[\begin{array}{c}#1 \\ #2 \\ #3 \end{array}\right]}\) \(\newcommand{\fourvec}[4]{\left[\begin{array}{r}#1 \\ #2 \\ #3 \\ #4 \end{array}\right]}\) \(\newcommand{\cfourvec}[4]{\left[\begin{array}{c}#1 \\ #2 \\ #3 \\ #4 \end{array}\right]}\) \(\newcommand{\fivevec}[5]{\left[\begin{array}{r}#1 \\ #2 \\ #3 \\ #4 \\ #5 \\ \end{array}\right]}\) \(\newcommand{\cfivevec}[5]{\left[\begin{array}{c}#1 \\ #2 \\ #3 \\ #4 \\ #5 \\ \end{array}\right]}\) \(\newcommand{\mattwo}[4]{\left[\begin{array}{rr}#1 \amp #2 \\ #3 \amp #4 \\ \end{array}\right]}\) \(\newcommand{\laspan}[1]{\text{Span}\{#1\}}\) \(\newcommand{\bcal}{\cal B}\) \(\newcommand{\ccal}{\cal C}\) \(\newcommand{\scal}{\cal S}\) \(\newcommand{\wcal}{\cal W}\) \(\newcommand{\ecal}{\cal E}\) \(\newcommand{\coords}[2]{\left\{#1\right\}_{#2}}\) \(\newcommand{\gray}[1]{\color{gray}{#1}}\) \(\newcommand{\lgray}[1]{\color{lightgray}{#1}}\) \(\newcommand{\rank}{\operatorname{rank}}\) \(\newcommand{\row}{\text{Row}}\) \(\newcommand{\col}{\text{Col}}\) \(\renewcommand{\row}{\text{Row}}\) \(\newcommand{\nul}{\text{Nul}}\) \(\newcommand{\var}{\text{Var}}\) \(\newcommand{\corr}{\text{corr}}\) \(\newcommand{\len}[1]{\left|#1\right|}\) \(\newcommand{\bbar}{\overline{\bvec}}\) \(\newcommand{\bhat}{\widehat{\bvec}}\) \(\newcommand{\bperp}{\bvec^\perp}\) \(\newcommand{\xhat}{\widehat{\xvec}}\) \(\newcommand{\vhat}{\widehat{\vvec}}\) \(\newcommand{\uhat}{\widehat{\uvec}}\) \(\newcommand{\what}{\widehat{\wvec}}\) \(\newcommand{\Sighat}{\widehat{\Sigma}}\) \(\newcommand{\lt}{<}\) \(\newcommand{\gt}{>}\) \(\newcommand{\amp}{&}\) \(\definecolor{fillinmathshade}{gray}{0.9}\)- Understand the terms used for costing purposes.
Question: Much of what we discuss in this book relates to companies that manufacture products, such as Nike and Apple, and terminology is a key component of accounting for manufacturing companies. The challenge is in classifying costs correctly for items such as production materials, production labor, marketing department labor, rent for production facilities, and rent for the administrative services facilities. These costs must be classified accurately so that they appear correctly in company financial reports. The starting point for learning how to classify costs correctly is in understanding two broad categories of costs. What are the two broad terms used to categorize cost information in a manufacturing setting?
- Answer
-
The two broad categories of costs are manufacturing costs and nonmanufacturing costs. Each category is described in detail as follows.
Manufacturing Costs
All costs related to the production of goods are called manufacturing costs16; they are also referred to as product costs17. A manufacturer purchases materials, employs workers who use the materials to assemble the goods, provides a building where the materials are stored and goods are assembled, and sells the goods. We classify the costs associated with these activities into three categories: direct materials, direct labor, and manufacturing overhead.
To help clarify which costs are included in these three categories, let’s look at a furniture company that specializes in building custom wood tables called Custom Furniture Company. Each table is unique and built to customer specifications for use in homes (coffee tables and dining room tables) and offices (boardroom and meeting room tables). The sales price of each table varies significantly, from $1,000 to more than $30,000. Figure 1.4 shows examples of production activities at Custom Furniture Company for each of the three categories (we continue using this company as an example in Chapter 2).
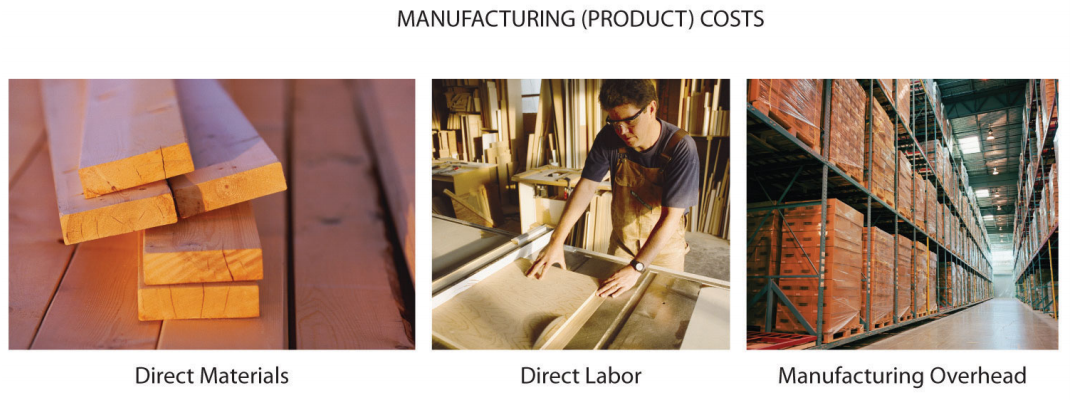
Direct Materials
Question: Raw materials used in the production process that are easily traced to the product are called direct materials18. What materials used in the production process at Custom Furniture would be classified as direct materials?
- Answer
-
The wood used to build tables and the hardware used to attach table legs would be considered direct materials. Small, inexpensive items like glue, nails, and masking tape are typically not included in direct materials because the cost of tracing these items to the product outweighs the benefit of having accurate cost data. These minor types of materials, often called supplies or indirect materials, are included in manufacturing overhead, which we define later.
Direct Labor
Question: Workers who convert materials into a finished product and whose time is easily traced to the product are called direct labor19. Who represents direct labor at Custom Furniture?
- Answer
-
Direct labor would include the workers who use the wood, hardware, glue, lacquer, and other materials to build tables.
Manufacturing Overhead
Question: All costs associated with the production process other than direct material costs and direct labor costs are called manufacturing overhead20. Terms synonymous with manufacturing overhead include factory overhead, factory burden, and overhead. What items are included in manufacturing overhead?
- Answer
-
Manufacturing overhead consists of the following:
- Indirect material costs21. The cost of materials necessary to manufacture a product that are not easily traced to the product or not worth tracing to the product.
- Indirect labor costs22. The cost of workers who are involved in the production process but whose time cannot easily be traced to the product. For example, supervisors in the production process who oversee several different products and are responsible for hiring employees, scheduling employees, and ordering materials are considered indirect labor.
- Other manufacturing costs. These are all other costs for items associated with the factory, including equipment maintenance, insurance, utilities, and depreciation.
Table 1.2 provides several examples of manufacturing costs at Custom Furniture Company by category.
Direct Materials |
|
---|---|
Direct Labor |
|
Manufacturing Overhead |
|
Note 1.43 "Business in Action 1.5" details the materials, labor, and manufacturing overhead at a company that has been producing boats since 1968.
MasterCraft produces boats for water skiers and wake boarders. Each boat produced incurs significant manufacturing costs. MasterCraft records these manufacturing costs as inventory on the balance sheet until the boats are sold, at which time the costs are transferred to cost of goods sold on the income statement.
Photo courtesy of Brian Miller, http://www.flickr.com/photos/13233728@N00/5155012186/
Examples of direct materials for each boat include the hull, engine, transmission, carpet, gauges, seats, windshield, and swim platform. Examples of indirect materials (part of manufacturing overhead) include glue, paint, and screws. Direct labor includes the production workers who assemble the boats and test them before they are shipped out. Indirect labor (part of manufacturing overhead) includes the production supervisors who oversee production for several different boats and product lines.
Manufacturing overhead includes the indirect materials and indirect labor mentioned previously. Other manufacturing overhead items are factory building rent, maintenance and depreciation for production equipment, factory utilities, and quality control testing.
Source: MasterCraft, “Home Page,” http://www.mastercraft.com.
Nonmanufacturing Costs
Costs that are not related to the production of goods are called nonmanufacturing costs23; they are also referred to as period costs24. These costs have two components—selling costs and general and administrative costs—which are described next. Examples of nonmanufacturing costs appear in Figure 1.5.
Selling Costs
Question: Costs incurred to obtain customer orders and provide customers with a finished product are called selling costs25. (They are also often called marketing costs or selling and advertising costs.) What activities would be classified as selling costs at Custom Furniture?
- Answer
-
Examples of selling costs include advertising, sales commissions, salaries for marketing and advertising personnel, office space for marketing and advertising personnel, finished goods storage costs, and shipping costs paid by the seller for products shipped to customers.
General and Administrative Costs
Question: Costs related to the overall management of an organization are called general and administrative costs26. What activities would be classified as general and administrative costs at Custom Furniture?
- Answer
-
Examples include personnel and support staff in the following areas: accounting, human resources, legal, executive, and information technology. Depreciation of office equipment and buildings associated with these areas would also be included as general and administrative costs. General and administrative costs are often simply called administrative costs.
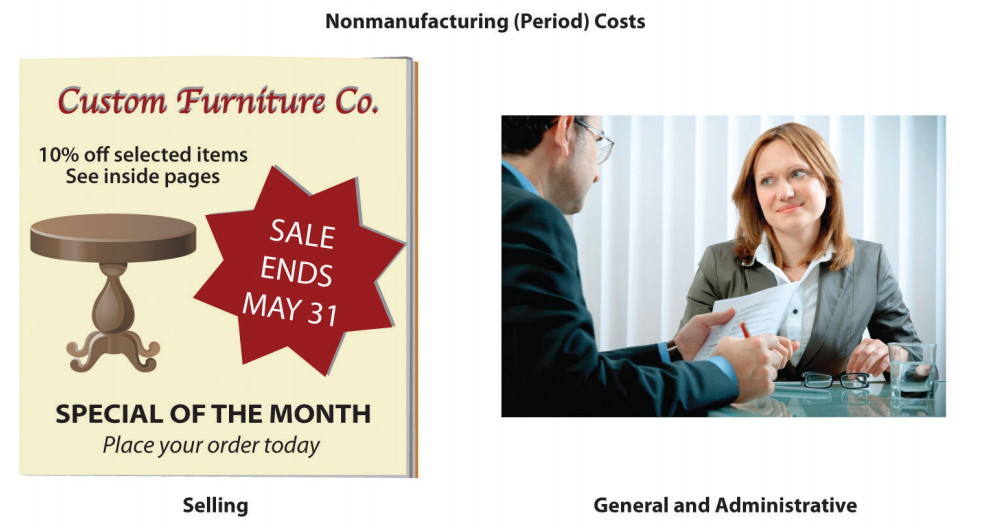
Although selling costs and general and administrative costs are considered nonmanufacturing costs, managers often want to assign some of these costs to products for decision-making purposes. For example, sales commissions and shipping costs for a specific product could be assigned to the product. This does not comply with U.S. GAAP because, under U.S. GAAP, only product costs can be assigned to products. However, as we noted earlier, managerial accounting information is tailored to meet the needs of the users and need not follow U.S. GAAP.
Distinguishing between manufacturing and nonmanufacturing costs is not always simple. For example, if legal staff works on an issue associated with production personnel and if human resources staff hires assembly line workers, are the costs involved manufacturing or nonmanufacturing costs? It is up to each organization to determine how to handle such costs for product costing purposes. The advantage of managerial accounting over financial accounting is that costs can be organized in any manner that helps managers make decisions. However, in this chapter, to avoid ambiguity, we follow the definitions provided by U.S. GAAP.
Presentation of Manufacturing and Nonmanufacturing Costs in Financial Statements
Question: At this point, you should be able to distinguish between manufacturing costs and nonmanufacturing costs. Why is it important to make this distinction?
- Answer
-
Distinguishing between the two categories is critical because the category determines where a cost will appear in the financial statements. All manufacturing costs (direct materials, direct labor, and manufacturing overhead) are attached to inventory as an asset on the balance sheet until the goods are sold, at which point the costs are transferred to cost of goods sold on the income statement as an expense. As we indicated earlier, nonmanufacturing costs are also called period costs; that is because they are expensed on the income statement in the time period in which they are incurred.
Table 1.3 clarifies the relationship between manufacturing and nonmanufacturing costs. It also describes the point at which these costs are recorded as expenses on the income statement. (Remember that the terms manufacturing cost and product cost are interchangeable, as are the terms nonmanufacturing cost and period cost.)
Manufacturing Costs (Also Called Product Costs) | Nonmanufacturing Costs (Also Called Period Costs) |
---|---|
|
|
Timing of expense: Costs are expensed when goods are sold. | Timing of expense: Costs are expensed during the time period incurred. |
Note 1.48 "Business in Action 1.6" provides examples of nonmanufacturing costs at PepsiCo, Inc.
PepsiCo, Inc., produces more than 500 products under several different brand names, including Frito-Lay, Pepsi-Cola, Gatorade, Tropicana, and Quaker. Net sales for 2010 totaled $57,800,000,000, resulting in operating profits of $6,300,000,000. Cost of sales represented the highest cost on the income statement at $26,600,000,000. The second highest cost on the income statement—selling and general and administrative expenses—totaled $22,800,000,000. These expenses are period costs, meaning they must be expensed in the period in which they are incurred.
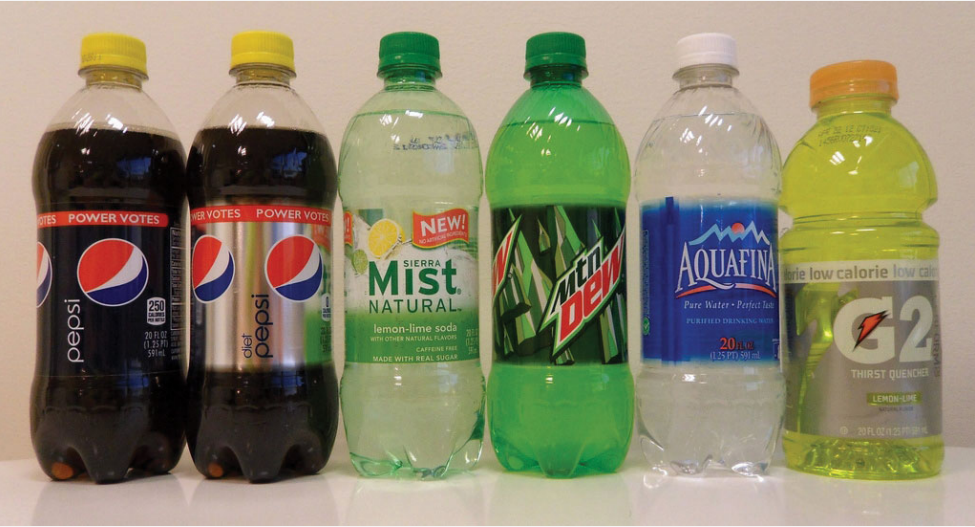
Examples of selling costs for PepsiCo include television advertising (probably the biggest piece of the $22,800,000,000), promotional coupons, costs of shipping products to customers, and salaries of marketing and advertising personnel.
Examples of general and administrative costs include salaries and bonuses of top executives and the costs of administrative departments, including personnel, accounting, legal, and information technology.
Source: PepsiCo, “PepsiCo 2010 Annual Report,” http://www.pepsico.com.
All manufacturing costs that are easily traceable to a product are classified as either direct materials or direct labor. All other manufacturing costs are classified as manufacturing overhead. All nonmanufacturing costs are not related to production and are classified as either selling costs or general and administrative costs.
- The following manufacturing items are for a construction company working on several custom homes. Identify whether each item should be categorized as direct materials, direct labor, or manufacturing overhead.
- Nails
- Lumber
- Drywall
- Workers building the house frame
- Supervisor responsible for three homes
- Light bulbs
- Cabinets
- Depreciation of construction equipment
- Identify whether each item in the following should be categorized as a product (manufacturing) cost or as period (nonmanufacturing) cost. Also indicate whether the cost should be recorded as an expense when the cost is incurred or as an expense when the goods are sold.
- Advertising
- Shipping costs for raw materials coming from a supplier
- Shipping costs for goods shipped to a customer
- Chief executive officer’s salary
- Production supervisor’s salary
- Depreciation on production equipment
- Raw materials used in production
- Paper used by the accounting staff
- Commissions paid to salespeople
- Janitorial services provided for production facility
- Supplies used by human resources personnel
- Utility costs for retail store
- Insurance costs for production facility
- Assembly line workers
- Clerical support for chief executive officer
- Maintenance of production equipment
- Identify whether each item listed in item 2 should be categorized as direct materials, direct labor, manufacturing overhead, selling cost, or general and administrative cost.
- Answer
-
-
- Manufacturing overhead
- Direct materials
- Direct materials
- Direct labor
- Manufacturing overhead
- Manufacturing overhead (You might call this a direct material, but the benefit of tracking this item as a direct material probably does not outweigh the cost.)
- Direct materials
- Manufacturing overhead
-
- Period cost, expensed when incurred
- Product cost, expensed when goods are sold
- Period cost, expensed when incurred
- Period cost, expensed when incurred
- Product cost, expensed when goods are sold
- Product cost, expensed when goods are sold
- Product cost, expensed when goods are sold
- Period cost, expensed when incurred
- Period cost, expensed when incurred
- Product cost, expensed when goods are sold
- Period cost, expensed when incurred
- Period cost, expensed when incurred
- Product cost, expensed when goods are sold
- Product cost, expensed when goods are sold
- Period cost, expensed when incurred
- Product cost, expensed when goods are sold
-
- Selling
- Direct materials or manufacturing overhead, depending on if the materials are easily traced to the product (direct) or not (indirect manufacturing overhead)
- Selling
- General and administrative
- Manufacturing overhead
- Manufacturing overhead
- Direct materials or manufacturing overhead, depending on if the materials are easily traced to the product (direct) or not (indirect manufacturing overhead)
- General and administrative
- Selling
- Manufacturing overhead
- General and administrative
- Selling
- Manufacturing overhead
- Direct labor
- General and administrative
- Manufacturing overhead
-
Definitions
- All costs related to the production of goods; also called product costs
- All costs related to the production of goods; also called manufacturing costs.
- Raw materials used in the production process that are easily traced to the product.
- Labor performed by workers who convert materials into a finished product and whose time is easily traced to the product.
- All costs associated with the production process other than direct material costs and direct labor costs.
- The costs of materials necessary to manufacture a product that are not easily traced to the product or that are not worth tracing to the product.
- The costs of workers who are involved in the production process but whose time cannot easily be traced to the product.
- Costs that are not related to the production of goods; also called period costs.
- Costs that are not related to the production of goods; also called nonmanufacturing costs.
- Costs incurred to obtain customer orders and provide customers with a finished product.
- Costs related to the overall management of an organization.